Catalytic Sensors: Principles, Applications, and Performance
1. Introduction
Catalytic sensors, also known as pellistor sensors, are widely used for the detection of flammable gases such as methane, propane, hydrogen, and butane. Due to their robust design, low cost, and effectiveness in explosive atmospheres, they are a go-to technology in industrial safety systems, gas detectors, and explosion protection equipment.
2. What Is a Catalytic Sensor?
A catalytic sensor is a type of gas sensor that detects combustible gases by oxidizing them on a heated catalytic bead, producing heat, which changes the bead’s electrical resistance. This change is measured and interpreted as the gas concentration.
3. History and Development
Catalytic sensors were first introduced in the early 20th century, originally developed for coal mining safety to detect methane. Over the decades, their design and materials have evolved to improve stability, selectivity, and durability, making them a mainstay in fixed and portable gas detection devices.
4. Working Principle of Catalytic Combustion
.jpg)
The core of a catalytic sensor operates on the principle of combustion:
- Combustible gas diffuses into the sensor chamber.
- A heated catalyst bead oxidizes the gas at low concentrations.
- The exothermic reaction generates heat.
- This heat changes the resistance of a platinum coil embedded in the catalyst.
- The change in resistance is proportional to the concentration of the gas.
The sensor is often configured as a Wheatstone bridge, allowing precise measurement of differential resistance between an active and a reference bead.
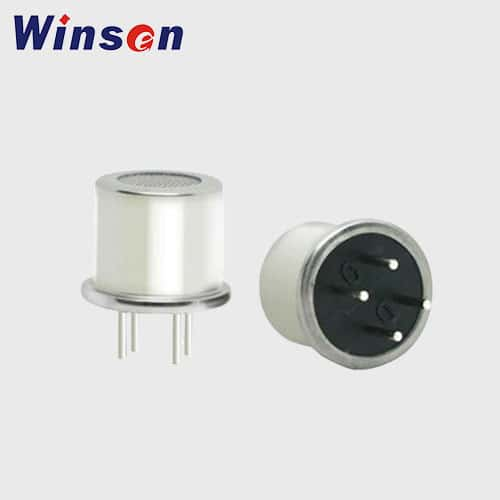
MR007 CH4 Methane C3H8 Propane Gas Sensor
- CH4 methane C3H8 propane, combustible gas, natural gas, coal gas, LPG gas
- 0~100 LEL
- Read More
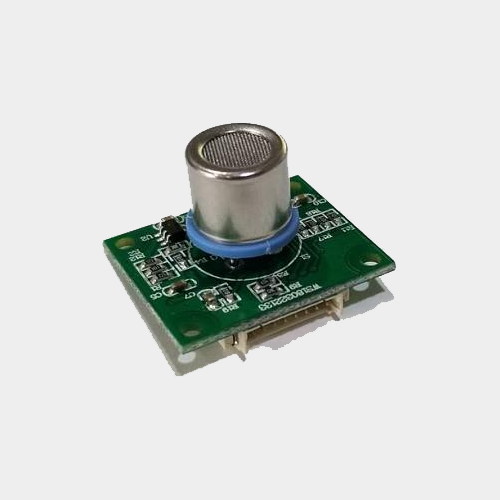
ZC13 Methane CH4 Sensor Module for Home Gas Safety
- methane CH4, natural gas, flammable gas
- 1%-25%LEL,Resolution100ppm
- Read More
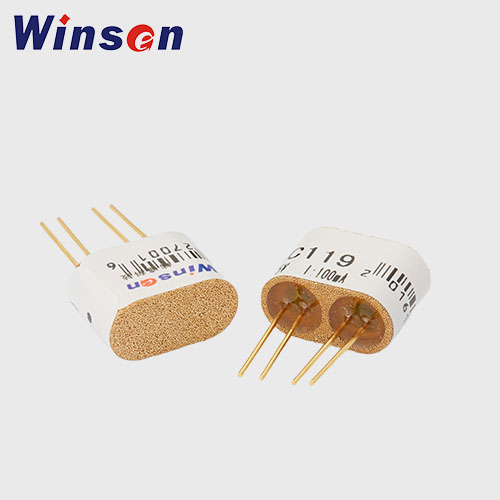
MC119 Catalytic Flammable Gas Sensor
- hydrogen, acetylene, gasoline, VOC such as alcohol, ketone, benzene.
- 0-100%LEL Anti-explosion Mark:ExdibⅠ
- Read More
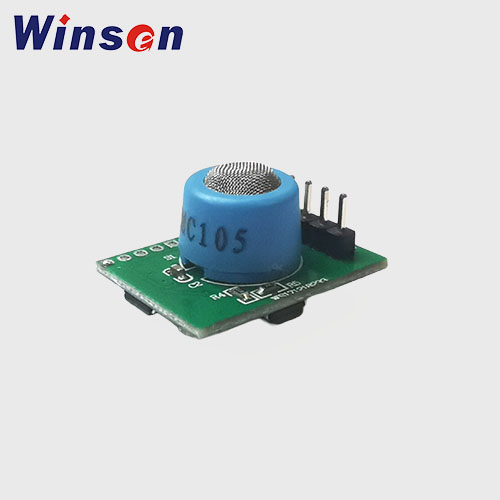
ZC08-CH4 Methane Sensor Module for Home Natural Gas Leakage
- methane CH4, natural gas, flammable gas
- 1%-20%LEL,Resolution100ppm
- Read More
5. Structure and Components
A catalytic sensor usually consists of the following:
- Active Bead: Coated with a catalyst like platinum or palladium.
- Reference Bead: Inert material, same heat capacity but no catalyst.
- Platinum Coil: Embedded inside both beads, functions as a heating element and resistance sensor.
- Stainless Steel Housing: Perforated to allow gas diffusion.
- Flame Arrestor: Prevents ignition outside the sensor in explosive atmospheres.
- Signal Conditioning Circuit: Converts resistance changes to a readable output.
6. Catalytic vs. Other Gas Sensor Types
Feature | Catalytic Sensor | Infrared (IR) | Semiconductor | Electrochemical |
---|---|---|---|---|
Gas Types | Combustibles | Combustibles | VOCs, combustibles | Toxic gases |
Response Time | Fast (~5-15s) | Moderate | Fast | Slow (~30-60s) |
Humidity Sensitivity | Moderate | Low | High | High |
Cost | Low | High | Low | Moderate |
Lifespan | ~2–5 years | ~5–10 years | ~2 years | ~1–2 years |
Intrinsically Safe | Yes (with arrestor) | Yes | Yes | Yes |
7. Detection Mechanism for Flammable Gases
Catalytic sensors typically detect gases that:
- Have explosive limits (LEL and UEL).
- Undergo oxidation at moderate temperatures.
- Are present in air or oxygen-rich environments.
Typical gases include:
- Methane (CH₄)
- Propane (C₃H₈)
- Butane (C₄H₁₀)
- Hydrogen (H₂)
- Ethanol, Acetone, and other hydrocarbons
8. Calibration and Signal Output
Catalytic sensors require calibration against known gas standards, usually expressed in terms of %LEL (Lower Explosive Limit).
- Signal Output: Voltage proportional to gas concentration.
- Linear Range: 0 – 100% LEL.
- Calibration Frequency: Every 3–6 months for best accuracy.
9. Advantages of Catalytic Sensors
Wide Detection Range (0–100% LEL)
Fast Response Time
Simple and Robust Design
Cost-Effective
Good Linearity
Stable in Harsh Environments (with proper design)
Low Power Requirements
Reliable in Mixed Gas Environments
10. Limitations and Challenges
Requires oxygen for combustion (not suitable for inert atmospheres)
Can be poisoned by chemicals like silicone, sulfur, lead
Cross-sensitivity to other combustibles
Heat-sensitive; not ideal for high-temperature environments
Needs frequent calibration and preventive maintenance
11. Typical Gases Detected
Gas | LEL (%) | Detected by Catalytic Sensor? |
---|---|---|
Methane | 5 | Yes |
Propane | 2.1 | Yes |
Hydrogen | 4 | Yes |
Ethanol | 3.3 | Yes |
Carbon Monoxide (CO) | – | No |
Ammonia (NH₃) | 15 | Partial |
Acetylene | 2.5 | Yes |
12. Applications Across Industries
- Oil and Gas: Leak detection in refineries, pipelines, and rigs
- Chemical Plants: Safety monitoring around reactors and tanks
- Mining: Methane detection in coal mines
- Manufacturing: VOC detection in painting or solvent areas
- Utilities: Gas leak detection in city pipelines
- Confined Space Entry: Worker safety in tanks, vessels, and pits
- Waste Management: Methane monitoring in landfills and digesters
13. Factors Affecting Performance
- Oxygen concentration: Needs ~15–21% for optimal function
- Temperature: Typical range −40°C to +70°C
- Humidity: High humidity can cause condensation
- Dust or Oil Contamination: Can block gas diffusion
- Sensor Poisoning: From leaded fuels, silicones, phosphates
14. Maintenance and Lifespan
Typical lifespan: 2–5 years under normal conditions.
Maintenance best practices:
- Monthly bump test
- Calibration every 3–6 months
- Filter cleaning/replacement
- Sensor replacement upon loss of response or poisoning
15. Safety Considerations
- Catalytic sensors should be housed in intrinsically safe enclosures.
- Must have flame arrestors to prevent ignition.
- Should comply with ATEX, IECEx, or UL certifications for explosive environments.
- Not suitable for oxygen-deficient areas.
16. Environmental Sensitivity
- Humidity: Can affect baseline signal
- Pressure changes: Alter gas diffusion rate
- Wind speed/airflow: May cool sensor bead
- Altitude: Reduces oxygen concentration
17. Recent Innovations in Catalytic Sensors
- Micro Pellistors: Miniaturized sensors with lower power consumption
- Hybrid Designs: Combining catalytic with infrared or MEMS sensors
- Digital Output Sensors: Integrated signal conditioning electronics
- Poison-Resistant Coatings: To extend life in industrial environments
- Wireless Sensor Integration: For smart gas detection systems
18. Comparison Table: Catalytic vs. Infrared (IR) Sensors
Feature | Catalytic Sensor | IR Sensor |
---|---|---|
Flammable Gas Detection | All hydrocarbon gases | Hydrocarbon only |
Requires Oxygen | Yes | No |
Poisoning Risk | Yes | No |
Maintenance Frequency | Higher | Lower |
Cost | Lower | Higher |
Lifespan | 2–5 years | 5–10 years |
Gas Specificity | Low (broad) | High (narrowband filter) |
19. Frequently Asked Questions (FAQs)
Q1: Can a catalytic sensor detect hydrogen?
Yes. Catalytic sensors can detect hydrogen efficiently, but cross-sensitivity must be managed.
Q2: Is it safe to use in an explosive environment?
Yes, with proper housing and flame arrestors, catalytic sensors are intrinsically safe.
Q3: What gases can poison a catalytic sensor?
Silicones, sulfur compounds, chlorinated hydrocarbons, lead, and phosphates.
Q4: How often should I calibrate the sensor?
Typically every 3–6 months, depending on usage and environmental exposure.
Q5: Can it be used in oxygen-deficient areas?
No. Catalytic sensors require oxygen for combustion and will not function reliably below ~10–15% O₂.
20. Conclusion
Catalytic sensors remain a cornerstone in combustible gas detection due to their simplicity, reliability, and cost-efficiency. While newer technologies like infrared and MEMS sensors have emerged, catalytic sensors continue to offer unparalleled performance for general-purpose flammable gas detection across a wide range of industries.
Their limitations—such as susceptibility to poisoning and oxygen dependency—are important to manage through proper selection, calibration, and maintenance.
Whether in oil fields, manufacturing plants, or confined spaces, catalytic sensors help safeguard lives and infrastructure by providing early warning of explosive gas concentrations.